Energiekosten bei Isolierung von Synthesekautschuk halbiert
Kautschuk ist ein gefragter Rohstoff, vor allem für Autoreifen, aber auch für Gummiprodukte und Matratzen. Nicht zuletzt weil das Angebot an Naturkautschuk schwankt, ist synthetisch hergestellter Kautschuk eine wichtige Alternative. Um diesen vom im Herstellungsprozess notwendigen Lösungsmittel zu isolieren, ist in der Regel viel Energie aufzuwenden. Hierfür entwickelte das Fraunhofer-Pilotanlagenzentrum für Polymersynthese und -verarbeitung PAZ in Schkopau gemeinsam mit dem Schweizer Unternehmen List AG ein innovatives Verfahren weiter. Ergebnis: eine Kostenreduktion von durchschnittlich 50 Prozent durch den Einsatz von Niederdruckdampf.
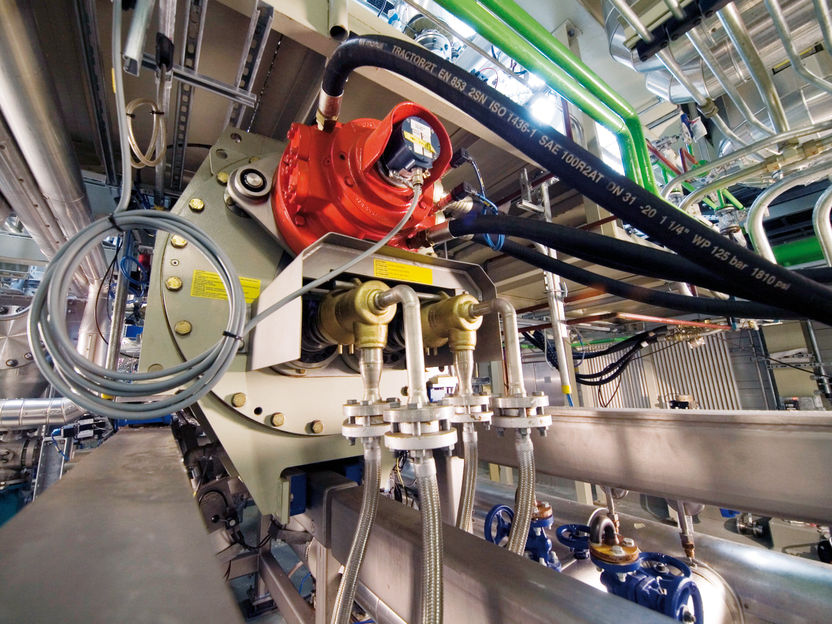
Im Knetreaktor wird synthetisch hergestellter Kautschuk von seinem Lösungsmittel getrennt. Am Fraunhofer PAZ sind solche Anlagen sowohl im Labor- als auch im Technikumsmaßstab verfügbar.
© Foto Fraunhofer IAP, Fotograf: Alexander Krause
Moderner synthetischer Kautschuk wird mittels Lösungspolymerisation hergestellt. Das Lösungsmittel ist vom Kautschukpolymer nur aufwändig zu trennen, weil der Kautschuk durch seine ihm eigenen Doppelbindungen beim Einfluss von Hitze und mechanischer Belastung zur Vernetzung neigt. Diese ist zwar bei einem fertigen Autoreifen gewollt, im Produktionsprozess ist eine Vor-Vulkanisation jedoch ein unerwünschter Faktor. Um das Kautschukpolymer bei der Trennung von seinem Lösungsmittel zu schonen, werden am Fraunhofer PAZ, einer Gemeinschaftsanlage des Fraunhofer-Instituts für Angewandte Polymerforschung IAP in Potsdam-Golm und des Fraunhofer-Instituts für Mikrostruktur von Werkstoffen und Systemen IMWS in Halle, zwei Knetreaktoren eingesetzt. In einem mit der List AG entwickelten Verfahren wird dabei auf Direktverdampfung gesetzt. Die dadurch erzielte Energieeinsparung beträgt 75 Prozent, jedoch ging dies bislang mit dem hohen Einsatz von relativ teurer elektrischer Energie einher.
Dieses Verfahren wurde nun entscheidend weiterentwickelt. »Zwar sparte man bisher schon einen Großteil der eingesetzten Energie. Mit Blick auf die Wettbewerbsfähigkeit der Industrie haben wir uns nun aber auch die Kostenseite angesehen«, sagt Dr. Ulrich Wendler, Leiter Synthese und Produktentwicklung am Fraunhofer PAZ. Um den teuren Strom weitestgehend durch billige thermische Energie zu ersetzen, wurde in einem Forschungsprojekt ein zusätzlicher Prozessschritt eingeführt, der unter robusten Betriebsbedingungen und bei minimalen Investitionskosten eine Optimierung der Energiekostenstruktur zulässt. Durch den Einsatz von preiswertem Niederdruckdampf kann nun – abhängig von Material und Viskosität der eingesetzten Kautschuklösung – eine Energiekosteneinsparung von mehr als 50 Prozent erzielt werden.
Hintergrund des weiterentwickelten Verfahrens ist der Einsatz von Knetreaktoren, die mit dem Industriepartner List AG entwickelt wurden, in Kombination mit einer speziellen Aufkonzentrationstechnologie für temperatursensitive Polymerlösungen. In der herkömmlichen Koagulation wird über mehrere Stunden eine Hitze von etwa 100 Grad Celsius aufgewendet. In der bereits 2007 entwickelten Isolierung von Kautschukpolymeren, bedarf es bei der Aufarbeitung im Knetreaktor lediglich einer Temperatur im Bereich von 70-90 Grad Celsius bei einer Verweilzeit von nur 30 Minuten. Durch die eingesetzte Technologie werden die stofflichen Eigenschaften des Werkstoffs nur extrem wenig beeinträchtigt. Ein weiterer Vorteil im Verfahren ist, dass fast ausschließlich wasserfreies Lösungsmittel anfällt. Somit kann der aufwändige Prozess zur Trocknung des Lösungsmittels deutlich optimiert werden, was zusätzliche Kosteneinsparungen ermöglicht. »Durch das von uns entwickelte Verfahren konnten wir einen erheblichen Fortschritt bei der Isolierung von Kautschukpolymeren erreichen. Diesen Prozess haben wir über die Jahre besser verstanden«, sagt Ulrich Wendler rückblickend.
Grundlage für diese Optimierung ist nach Aussage von Wendler die Möglichkeit, Informationen aus dem Pilotmaßstab in eine industrienahe Größe zu skalieren – genau dafür biete das Fraunhofer PAZ die passenden Anlagen und das nötige Knowhow. Die Prozessdaten werden sowohl im Labormaßstab (Kneter mit einem Volumen von 2,5 Liter und 4 Liter) wie auch im Pilotmaßstab (100 Liter und 200 Liter) ermittelt. »Erst bei der Betrachtung der Maßstabsübertragungen über zwei Zehnerpotenzen zeigen sich die wahren prozessualen wie stofflichen Herausforderungen«, erklärt er. Nur mit einer solchen Herangehensweise ließen sich größere Mengen eines neu entwickelten Materials sicher und ohne Prozessrisiken hervorbringen. Laut Wendler eine ganz wichtige und erprobte Herangehensweise, um neue Technologien in den Produktionsmaßstab zu überführen: »Durch die sichere Beherrschung der Skalierung in zwei, deutlich voneinander unterscheidbaren Apparategrößen, kann man das Prozessrisiko für den großtechnischen Maßstab signifikant minimieren.«