LANXESS erhält Auszeichnung
Spezialchemie-Konzern gewinnt ersten Preis beim „Responsible Care“-Wettbewerb des VCI NRW
Der Spezialchemie-Konzern LANXESS ist für sein Engagement für nachhaltige Produktionsprozesse ausgezeichnet worden: Das so genannte „Dry Finishing“-Verfahren zur umwelt- und ressourcenschonenden Gewinnung von Butylkautschuk siegte beim diesjährigen „Responsible Care“-Wettbewerb des Verbands der Chemischen Industrie (VCI) in Nordrhein-Westfalen. Mitarbeiter des LANXESS-Geschäftsbereichs Butyl Rubber haben das Verfahren zusammen mit Kollegen aus dem Zentralbereich „Innovation & Technology“ entwickelt. „Responsible Care“ ist eine internationale Initiative der Chemischen Industrie. Sie hat zum Ziel, die Bedingungen für den Schutz von Gesundheit und Umwelt sowie für Sicherheit von Mitarbeitern und Nachbarschaft ständig zu verbessern – unabhängig von gesetzlichen Vorgaben. Der Preis wurde gestern Abend im Rahmen des Parlamentarischen Abends des VCI in Düsseldorf überreicht.
„Mit dem ‚Dry Finishing’-Verfahren können wir den Herstellungsprozess von hochwertigem Butylkautschuk deutlich optimieren“, sagte Hanns-Ingolf Paul, Leiter Global Technology des LANXESS-Geschäftsbereichs Butyl Rubber. „Es reduziert die Zahl der Projektschritte, gleichzeitig senkt es Strom- und Dampfeinsatz sowie die während der Produktion entstehenden Abluft- und Abwassermengen. Das innovative Verfahren ermöglicht einen modernen, noch saubereren Herstellungsprozess, der auch für andere Synthesekautschuke verwendbar ist“, so Paul, der den Preis stellvertretend für alle Beteiligten entgegennahm.
Weniger Projektschritte, geringerer Energieverbrauch
Ein wesentlicher Fortschritt des „Dry Finishing“-Verfahrens gegenüber der herkömmlichen Produktion von Synthesekautschuk ist der Verzicht auf das prozess- und energieintensive so genannte Dampf-Strippen, das die flüssige Kautschuk-Lösung in einen festen Aggregatzustand überführt. Die Entgasung der Lösung erfolgt stattdessen per Direkt-Eindampfverfahren in einem speziellen Extrusionsapparat. Dort findet auch die Trocknung des Synthesekautschuks in einer Zentrifuge statt. Bislang erfolgt dieser Produktionsschritt über Trockenbänder, die sowohl viel Energie verbrauchen als auch große Mengen an Abluft erzeugen. Das bei der Trocknung abgesonderte Wasser wird in den Produktionsprozess zurückgeführt.
Jury lobt breiten Anwendungsbereich
Neben der erheblichen Energieeinsparung war für die Jury entscheidend, dass die neue Technologie auch für die Herstellung anderer Synthesekautschuke genutzt werden kann und im Hinblick auf die Investitionen wettbewerbsfähig ist. „Die Vorteile dieser Technologie können somit faktisch auch einen breiteren Anwendungsbereich haben“, lautete die Urteilsbegründung.
Meistgelesene News
Organisationen
Weitere News aus dem Ressort Forschung & Entwicklung
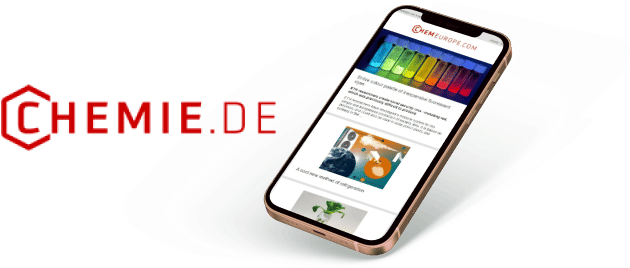
Holen Sie sich die Chemie-Branche in Ihren Posteingang
Mit dem Absenden des Formulars willigen Sie ein, dass Ihnen die LUMITOS AG den oder die oben ausgewählten Newsletter per E-Mail zusendet. Ihre Daten werden nicht an Dritte weitergegeben. Die Speicherung und Verarbeitung Ihrer Daten durch die LUMITOS AG erfolgt auf Basis unserer Datenschutzerklärung. LUMITOS darf Sie zum Zwecke der Werbung oder der Markt- und Meinungsforschung per E-Mail kontaktieren. Ihre Einwilligung können Sie jederzeit ohne Angabe von Gründen gegenüber der LUMITOS AG, Ernst-Augustin-Str. 2, 12489 Berlin oder per E-Mail unter widerruf@lumitos.com mit Wirkung für die Zukunft widerrufen. Zudem ist in jeder E-Mail ein Link zur Abbestellung des entsprechenden Newsletters enthalten.