Risiko Wasserstoffversprödung bewerten
Neue Simulation zur Kaltrissbildung bei hochfesten Stählen
Hochfeste Stähle spielen im modernen Fahrzeug- und Maschinenbau eine wesentliche Rolle. Werden diese Stähle bei der Herstellung von Bauteilen geschweißt, können bewegliche Wasserstoff-Atome im Material Probleme verursachen: Die Atome sammeln sich langsam an Bauteilbereichen mit hohen Eigenspannungen an und machen dort den Stahl spröde. Die Folge sind sogenannte Kaltrisse, die für Bauteilausschuss sorgen können. Dr. Frank Schweizer vom Fraunhofer-Institut für Werkstoffmechanik IWM hat nun eine Simulations-Methodik entwickelt, mit der Bauteilhersteller diese Kaltrissneigung bewerten und ihre Produktion entsprechend anpassen können.
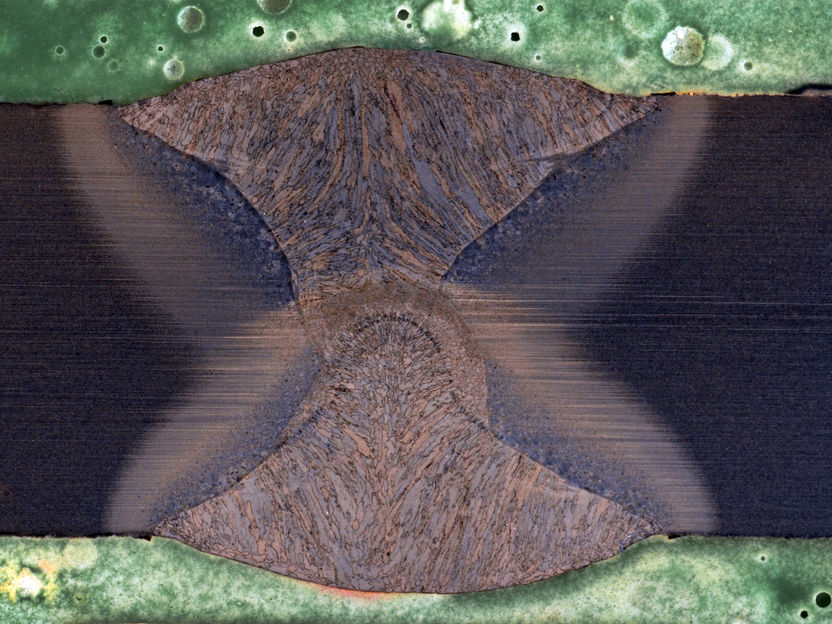
Lichtmikroskopische Aufnahme des Schweißnahtgefüges einer Schweißverbindung.
© Fraunhofer IWM
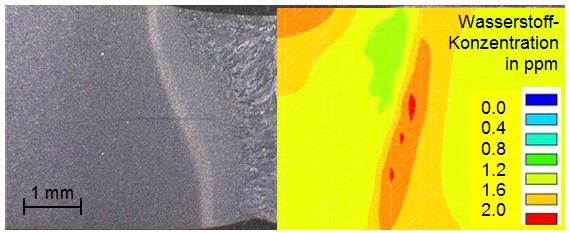
Die neue Simulationsmethode hilft, Laserschweißprozesse zu optimieren: Lichtmikroskopische Aufnahme des Schweißnahtgefüges einer Laserschweißverbindung (links) im Vergleich mit der berechneten lokalen diffusiblen Wasserstoffkonzentration in Abhängigkeit von Temperatur-Zeit-Verlauf und Schweißeigenspannungen (rechts).
© Fraunhofer IWM
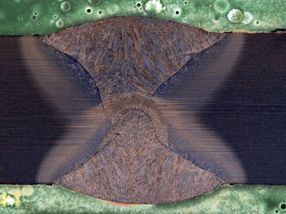
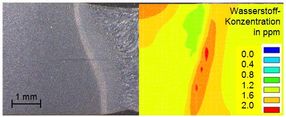
Die Hersteller von Fahrzeug- und Maschinenbauteilen nutzen häufig hochfeste Stähle: zur Materialeinsparung für den Leichtbau und für crashrelevante Strukturbauteile, die besonders hohe Festigkeiten benötigen. Beim Schweißen dieser Bauteile tragen vielfältige Faktoren dazu bei, dass sich ungewollt feine Risse bilden können, sich ausbreiten und sogar möglicherweise zu Bauteilausschuss führen. Diese Faktoren sind leider nur sehr schwer oder gar nicht durch Experimente zu erfassen, beispielsweise müsste die Wasserstoffkonzentration an stark eingegrenzten Orten im Bauteilinneren während des Schweißens gemessen werden können. Eine weitere Schwierigkeit: Die Zeitspanne, in der die Risse entstehen, ist vergleichsweise lang – sie können während des Schweißens innerhalb weniger Sekunden oder auch noch nach mehreren Tagen danach auftreten. Bis heute gibt es aus diesen Gründen auch bei lasergeschweißten Bauteilen aus hochfesten Stählen häufig eine unangenehm hohe Ausschussrate in der Fertigung.
Einfluss von Wasserstofffallen abgebildet
Damit Bauteilhersteller die Ausschussrate bei hochfesten Stählen verringern können, hat Dr. Frank Schweizer aus der Gruppe »Mikrostruktur, Eigenspannungen« des Fraunhofer IWM im Rahmen seiner Dissertation bereits industriell eingesetzte Methoden der numerischen Schweißsimulation entsprechend weiterentwickelt. Damit kann er nun im Computer die Geschehnisse an ganz begrenzten Bauteilorten nachstellen. Das funktioniert sogar für sehr schnelle Temperaturwechsel zwischen Raum- und Schmelztemperatur, wie sie beim Schweißen auftreten. »Jetzt können wir die zeitliche Entwicklung der Einflussfaktoren und ihre Wechselwirkungen untereinander genau berechnen und virtuell beobachten«, erklärt Schweizer. Es sind Faktoren wie Härtegefüge, Eigenspannungen und die lokale Wasserstoffkonzentration, die im geschweißten Bauteil zur Rissbildung führen können. Neben dem zusätzlich eingebrachten Wasserstoff aus dem Schweißprozess löst sich durch die Schweißwärme der bereits im Stahl vorhandene Wasserstoff und wird beweglich beziehungsweise diffusionsfähig.
»Die Besonderheit an der neuen Methode ist, dass sie auch die Wirkung sogenannter Wasserstofffallen berücksichtigt«, so Schweizer. Er fand für unterschiedliche Laserschweißverbindungen heraus, dass bei geringen Wasserstoffkonzentrationen die Wasserstofffallen einen großen Einfluss auf den »beweglichen« Wasserstoffanteil haben. Bei höherem Wasserstoffgehalt wird das thermomechanische Materialverhalten zunehmend ausschlaggebend für die Rissbildung. »Die Wasserstoffatome sammeln sich langsam in dem schmalen Bereich der Wärmeeinflusszone an, in dem besonders hohe Zugeigenspannungen vorherrschen«, sagt Schweizer. Auch noch nachdem der Stahl abgekühlt ist, kann sich der Wasserstoff dann an diesen Stellen sammeln und das Material spröde machen. »Somit können auch noch nach Stunden und Tagen Risse entstehen, die das Aussortieren des Bauteils nötig machen«, erklärt Schweizer.
Simulation als Basis für die Optimierung des Laserschweißprozesses
Die Simulationsergebnisse dienen als Grundlage, Laserschweißprozesse zu optimieren und Bauteilausschuss nachhaltig zu verhindern: »Die Laser-Prozessparameter lassen sich nun so anpassen, dass die Wechselwirkungen der Kaltriss-Risikofaktoren so gering wie möglich bleiben«, sagt Schweizer. Auch genauere Vor- und Nachwärmtemperaturen sowie die passgenaue Glühdauer kann aus der Simulation ermittelt werden. »Auch bei der Planung von Bauteilen nutzt die Simulation: Anhand der Daten lassen sich günstigere Bauteilformen ableiten, um den Eigenspannungszustand lokal zu verbessern und Risse zu vermeiden«, erläutert Schweizer. In einem nächsten Forschungsschritt will er den Einfluss unterschiedlicher Werkstoffe und Bauteiloberflächen auf die sogenannte Effusion des Wasserstoffs genauer untersuchen, um Vor- und Nachwärmprozeduren zukünftig noch präziser auslegen zu können. Zudem wird er die neue Methodik auf weitere Stähle und andere Schweißverfahren anwenden.
Als Datengrundlage für die von Schweizer erweiterten numerischen Schweißsimulationen dienten charakteristische Werkstoffkennwerte dreier unterschiedlicher hochfester Stähle: eines Wälzlager-, eines Martensitphasen- und eines Feinkornbaustahls. Diese charakteristischen Werkstoffkennwerte ermittelte er sowohl experimentell als auch mit neuen und eigenen rechnerischen Auswertemethoden. Seine Simulationsmodelle testete Schweizer erfolgreich an drei industriell eingesetzten Bauteilen, die mit verschiedenen Schweißverfahren gefügt wurden: dem Wärmeleitschweißen sowie dem Tiefschweißen per Faserlaser und CO2-Laser.