Ausweg aus dem Chrom-Verbot
Neue Beschichtungstechnik schützt vor Korrosion und Verschleiß
Sollen Bauteile weder korrodieren noch verschleißen, werden sie vielfach unter Einsatz von hexavalentem Chrom überzogen. Ab September 2017 ist dies jedoch nur noch mit Ausnahmeregelungen erlaubt. Das von Fraunhofer- und RWTH-Forschenden entwickelte extreme Hochgeschwindigkeits-Laserauftragschweißen EHLA bietet erstmals eine wirtschaftliche Alternative.
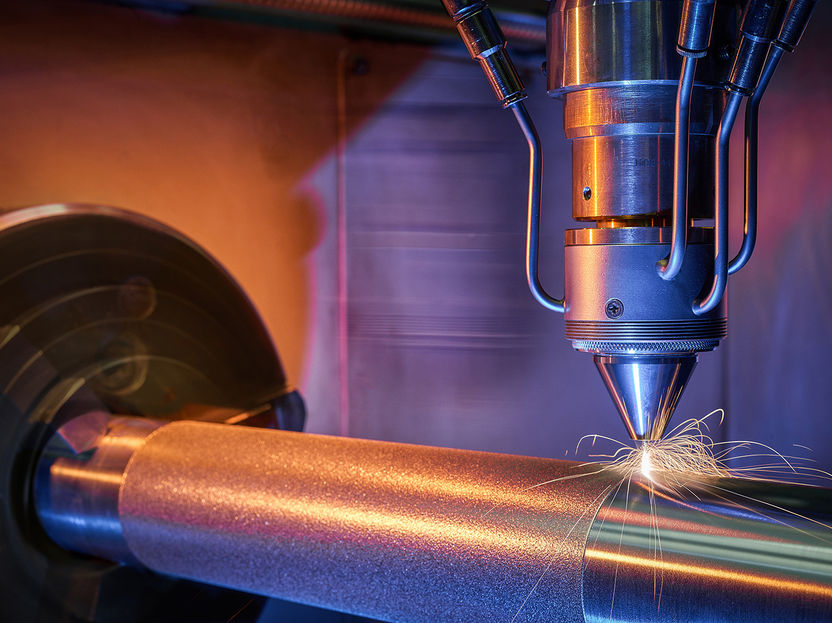
Mit EHLA lassen sich Metallschutzschichten mit extremer Hochgeschwindigkeit aufbringen.
© Foto Fraunhofer ILT, Aachen / Volker Lannert
Sei es in der Automobilindustrie, dem Maschinen- und Anlagenbau oder der Luft- und Raumfahrt – zahlreiche metallische Bauteile müssen vor Korrosion und Verschleiß geschützt werden. Eine gängige Methode dafür ist das Hartverchromen. Dieses Verfahren hat jedoch gravierende Nachteile: Es verbraucht nicht nur viel Energie, das dabei eingesetzte Chrom(VI) ist zudem stark umweltschädigend. Ab September2017 darf es daher nur noch nach Autorisierung/Zulassung verwendet werden. Dieses Verbot stellt die Industrie vor enorme Herausforderungen.
Wirtschaftliche Alternative zu Chrom(VI)
Dr.-Ing. Andres Gasser und Dipl.-Ing Thomas Schopphoven vom Fraunhofer-Institut für Lasertechnik ILT in Aachen und ihr Kollege Dipl.-Ing. Gerhard Maria Backes vom Lehrstuhl für Digital Additive Production der RWTH Aachen University haben nun eine wirtschaftliche Alternative entwickelt: Das extreme Hochgeschwindigkeits-Laserauftragschweißen, kurz EHLA. Dieses Verfahren bietet Unternehmen nicht nur einen Ausweg aus dem Verbots-Dilemma, sondern bringt zudem noch deutliche Vorteile gegenüber dem Hartverchromen mit sich: Es kommen keinerlei Chemikalien zum Einsatz – was das Verfahren sehr umweltfreundlich macht. Die entstehenden Schichten sind dicht und können das Bauteil somit wesentlich effizienter vor Korrosion und Verschleiß schützen. Zudem ist die Beschichtung stoffschlüssig mit dem Grundwerkstoff verbunden, so dass sie, anders als bei der Hartverchromung, nicht abplatzen kann. Für die neuen Beschichtungen können verschiedene Materialien verwendet werden, beispielsweise Eisen-, Nickel- und Kobalt-Basis-Legierungen.
Auch gegenüber dem thermischen Spritzen – einer anderen gängigen Art, Beschichtungen herzustellen – punktet das neuartige Verfahren: Statt lediglich etwa 50 Prozent des eingesetzten Materials gelangen rund 90 Prozent dorthin, wo sie gebraucht werden. Dies macht das Verfahren weitaus ressourcenschonender und somit deutlich wirtschaftlicher. »Mit dem EHLA-Verfahren können wir erstmalig dünne Schichten im Zehntel-Millimeter-Bereich auf große Flächen in kurzer Zeit ressourceneffizient auftragen«, fasst Dr.-Ing. Andres Gasser zusammen, der die Gruppe Laserauftragschweißen am Fraunhofer ILT leitet.
EHLA basiert auf dem Laserauftragschweißen, mit dem sich hochwertige Beschichtungen verschiedener Materialien herstellen lassen. Was den Verschleiß- und Korrosionsschutz angeht, konnte sich das Laserauftragschweißen bisher jedoch nur vereinzelt durchsetzen – es ist zu langsam. »Mit EHLA können wir das Bauteil mit Geschwindigkeiten beschichten, die 100- bis 250-mal über denen liegen, die beim konventionellen Laserauftragschweißen eingesetzt werden. Zudem heizt es sich kaum auf. Dadurch können wir auch hitzeempfindliche Komponenten beschichten«, weiß Dipl.-Ing. Gerhard Maria Backes. Weitere Vorteile: Die entstehende Schicht ist reiner und schützt besser vor Korrosion. Zudem werden gänzlich neue Materialkombinationen möglich, etwa Beschichtungen auf Aluminium- oder schwer schweißbaren Gusseisenlegierungen.
Nachhaltig, umweltfreundlich und arbeitsplatzsichernd
Bei einigen Unternehmen ist das neue Verfahren bereits im Einsatz. So etwa bei der niederländischen IHC Vremac Cylinders B.V., die ihre bis zu zehn Meter langen Hydraulik-Zylinder für Offshore-Anwendungen damit beschichten. Dipl.-Ing. Thomas Schopphoven sieht großes Potenzial für die neue Beschichtungstechnik: »Mit EHLA könnten wir in die Serienbeschichtung kommen – und künftig auch Bauteile beschichten, die bisher unbeschichtet eingesetzt wurden. Das ermöglicht neue Komponenten, die während des Produktlebenszyklus´ nicht mehr verschleißen. Zudem könnte EHLA die Beschichtungstechnik, die verstärkt in Niedriglohnländer abwandert, hier in Europa halten«.
Für die Entwicklung des EHLA-Verfahrens erhalten Dr.-Ing. Andres Gasser, Dipl.-Ing. Thomas Schopphoven und Dipl.-Ing. Gerhard Maria Backes den diesjährigen Joseph-von-Fraunhofer-Preis. Die Jury begründet die Preisvergabe unter anderem mit »der bereits erfolgten Umsetzung sowie dem wirtschaftlichen Ersatz von Chrom(VI) in wesentlichen Einsatzgebieten«.