Neuartiger hoch-produktiver Prozess für robuste Schichten auf flexiblen Materialien
Neue Forschungsergebnisse aus dem Bereich der Hochrate-Beschichtung
Wearables, gebogene Displays oder Gebäudefassaden fordern immer häufiger biegbare, flexible Oberflächen mit ganz bestimmten Funktionen oder Eigenschaften. Dazu gehören neben Schichten zur Verminderung der Gaspermeation, zum Schutz vor Chemikalien, Strahlung oder mechanischer Belastung auch leitfähige Schichten, oder Schichten mit speziellen optischen Eigenschaften. Diese werden durch Beschichtung der Oberflächen mit dünnen funktionalen Schichten erreicht. Die Erhöhung der Produktivität und der Effizienz der Beschichtungsprozesse ist ein wesentlicher Schwerpunkt der anwendungsnahen Forschung.
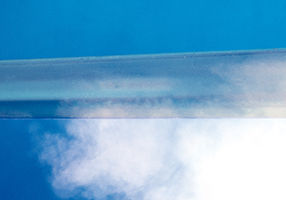
Folie mit transparenter Barriereschicht
Fraunhofer FEP
Ein solcher Beschichtungsprozess ist die plasmagestützte chemische Gasphasenabscheidung – PECVD. Das Fraunhofer FEP arbeitet verstärkt daran, PECVD-Prozesse für eine hohe Produktivität und den effizienten Einsatz in Rolle-zu-Rolle-Beschichtungsanlagen zu optimieren. Diese erlauben die großflächige, kosteneffiziente Beschichtung von flexiblem Trägermaterial. Im Gegensatz zu etablierten Verfahren setzt das Fraunhofer FEP auf Magnetrons und insbesondere Hohlkathoden als Plasmaquelle.
Michiel Top, Projektleiter im Bereich Flache und Flexible Produkte am Fraunhofer FEP, freut sich: „Mit dem hohlkathodengestützten PECVD-Prozess konnten wir ein breit einsetzbares Werkzeug zur Abscheidung von teilorganischen Plasmapolymerschichten auf flexiblen Substraten entwickeln, welches nicht nur Beschichtungsbreiten von bis zu 4 Metern erlaubt, sondern auch direkt mit anderen Verfahren wie Sputtern und Verdampfen in einer Anlage kombiniert werden kann.“
Für siliziumhaltige Plasmapolymerschichten wurden dynamische Beschichtungsraten bis zu 3000 Nanometer pro Meter und Minute erreicht. Dieser Wert liegt um einen Faktor 5-10 über dem, was etablierte Verfahren, wie z. B. die Mikrowellen-PECVD erreichen. Plasmapolymerschichten bieten einen guten Schutz für darunterliegende Funktionsschichten gegen chemischen Angriff (Säuren und Salze) oder gegen mechanische Beanspruchung, wie sie z. B. im Wickelprozess bei der weiteren Verarbeitung der Materialien in Rolle-zu-Rolle-Verfahren auftreten. Auch wurde nachgewiesen, dass die Wasserdampfdurchlässigkeit einer anorganischen Barriereschicht durch die Inline-Abscheidung einer polymerartigen Schutzschicht um bis zu 50 % verringert werden kann. Der Prozess erlaubt eine sehr feine Einstellung der Schichteigenschaften (Zusammensetzung, Härte oder Brechungsindex) und der Beschichtungsrate in einem vorgegebenen Rahmen. Dies ermöglicht z. B. in Kombination mit Sputterverfahren die Inline-Abscheidung mehrerer Schichten eines optischen Interferenzschichtsystems in einem Durchgang und spart so Prozessschritte und damit Geld.
Als nächste Aufgabe sehen die Forscher die weitere Optimierung des Prozesses und der Schichten für verschiedene Anwendungsszenarien z. B. in flexiblen elektronischen Bauelementen in enger Zusammenarbeit mit Industriepartnern im Maschinenbau, Beschichtungsdienstleistern und weiteren Anwendern. So lässt sich in naher Zukunft eine Überführung des Prozesses in die Produktion erreichen.
Meistgelesene News
Weitere News aus dem Ressort Wissenschaft
Diese Produkte könnten Sie interessieren
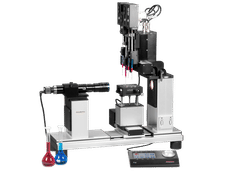
OCA 200 von DataPhysics
Mit Kontaktwinkelmesssystem Benetzung, Festkörper und Flüssigkeiten umfassend charakterisieren
Das OCA 200 löst mit intuitiver Software und modularem Aufbau individuelle Messaufgaben
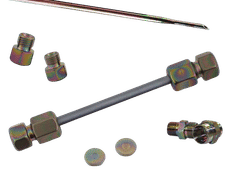
Dursan von SilcoTek
Innovative Beschichtung revolutioniert LC-Analytik
Edelstahlkomponenten mit der Leistung von PEEK – inert, robust und kostengünstig
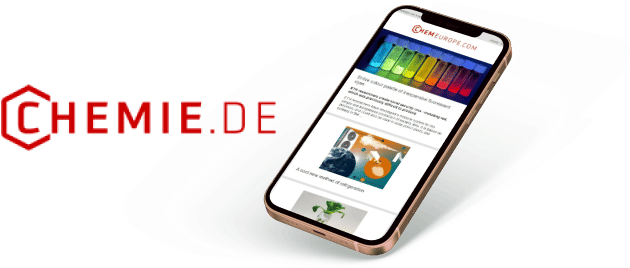
Holen Sie sich die Chemie-Branche in Ihren Posteingang
Mit dem Absenden des Formulars willigen Sie ein, dass Ihnen die LUMITOS AG den oder die oben ausgewählten Newsletter per E-Mail zusendet. Ihre Daten werden nicht an Dritte weitergegeben. Die Speicherung und Verarbeitung Ihrer Daten durch die LUMITOS AG erfolgt auf Basis unserer Datenschutzerklärung. LUMITOS darf Sie zum Zwecke der Werbung oder der Markt- und Meinungsforschung per E-Mail kontaktieren. Ihre Einwilligung können Sie jederzeit ohne Angabe von Gründen gegenüber der LUMITOS AG, Ernst-Augustin-Str. 2, 12489 Berlin oder per E-Mail unter widerruf@lumitos.com mit Wirkung für die Zukunft widerrufen. Zudem ist in jeder E-Mail ein Link zur Abbestellung des entsprechenden Newsletters enthalten.