Neuartiger Mikroreaktor für Grignard-Reagenzien
Kontinuierliche Prozessführung: Schneller, sicherer, sauberer
Victor Grignard erhielt 1912 den Nobelpreis für Chemie: Seither haben sich die nach ihm benannten Grignard-Reagenzien einen festen Platz in der chemischen und pharmazeutischen Industrie erobert. Ein neuartiger Mikroreaktor von Fraunhofer-Forschern lässt diese Reaktionen nun schneller und sicherer werden und die erzeugten Produkte reiner. Dazu kommt: Der Reaktor ist skalierbar und flexibel.
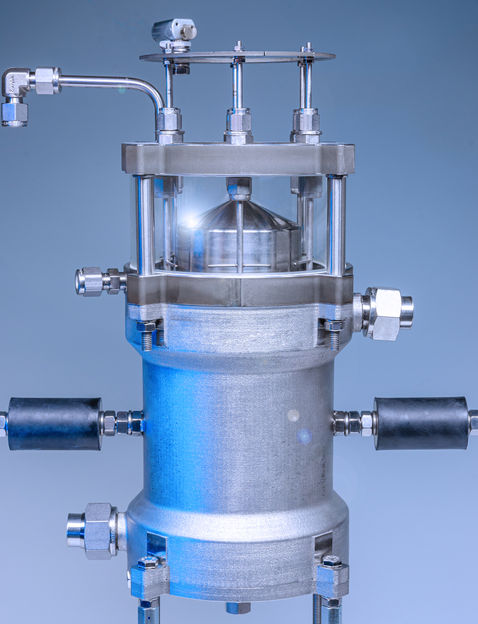
Einzelmodul zur Pilotierung der Grignard-Reagenzsynthese.
© Fraunhofer IMM
Pharmaka, Duftstoffe, Aromen: Diese Produkte werden vielfach über Grignard-Reagenzien hergestellt. Vor mehr als hundert Jahren entdeckt, sind diese Reaktionen eine der wirkungsvollsten Methoden, um chemische Bindungen zwischen Kohlenstoffatomen zu erzeugen. Was beispielsweise die Top 50 Pharmawirkstoffe angeht, so finden sich bei jedem zehnten Syntheseweg eine oder sogar mehrere Grignard-Reaktionen. Doch gibt es ein »Aber«: Zum einen dauert es je nach Reaktion unterschiedlich lang, bis diese in die Gänge kommt – dann allerdings entwickelt sich schnell sehr viel Hitze, die abgeführt werden muss. Um die Hitzeentwicklung zu begrenzen, gibt man das Reagenz immer nur portionsweise in den großen Rührkessel. Dies zieht die Reaktionszeiten in die Länge – zudem können sich in dieser Zeit viele Nebenprodukte bilden, die das entstehende Produkt verunreinigen. Zum Beispiel könnte es passieren, dass das Produkt, das man erhalten möchte, mit den zugesetzten Stoffen reagiert. Das Ergebnis sind Einbußen in Qualität oder Ausbeute.
Kontinuierliche Prozessführung: Schneller, sicherer, sauberer
Forscher des Fraunhofer-Instituts für Mikrotechnik und Mikrosysteme IMM in Mainz beseitigen diese Probleme. »Wir ersetzen den großen Rührkessel durch einen Durchflussreaktor«, sagt Dr. Gabriele Menges-Flanagan, Wissenschaftlerin am Fraunhofer IMM. »Auf diese Weise können wir die volle Macht der Reaktion ausnutzen und die Temperatur dennoch wunderbar kontrollieren.« Dieser Ansatz bringt mehrere Vorteile mit sich: Während die Reaktion im Rührkessel recht lange dauert, wird im Reaktor das gesamte Reagenz in nur wenigen Minuten umgewandelt. Zudem entsteht ein reineres Produkt und die produzierten Mengen lassen sich flexibel anpassen. Kurz gesagt: Der Prozess ist schneller, sicherer und das Produkt sauberer.
Möglich macht es der Aufbau des Reaktors. Die Ausgangssubstanz – meist ein organisches Bromid oder Chlorid – wird in einem Reaktor durch ein Bett aus Magnesiumspänen von unten nach oben gepumpt. Der große Überschuss an Magnesium im Durchflussreaktor ist wichtig, um die Reaktion in Schwung zu bringen und kontrollierter ablaufen zu lassen. Einer der Erfolgsgaranten ist die Geometrie des magnesiumgefüllten Reaktors: Es handelt sich um einen ringförmigen Zylinder, dessen Inneres und Äußeres mit durchlaufendem Öl gekühlt werden. Auf diese Weise kann die Reaktionswärme schnell und zuverlässig abgeführt werden – was nicht nur die Sicherheit erhöht, sondern auch weniger unerwünschte Nebenprodukte entstehen lässt. Die ständige Bewegung von Ausgangsstoff und Produkt durch den Reaktor unterdrückt Nebenreaktionen zusätzlich: Zum einen werden die Ausgangsstoffe in kurzer Zeit vollständig umgesetzt, zum anderen wird das entstehende Produkt ständig weiter durch den Reaktor bewegt, statt wie bisher im Rührkessel Seite an Seite mit den Ausgangsstoffen zu schwimmen. Es bieten sich somit schlichtweg weniger Möglichkeiten, miteinander zu reagieren. Der große Magnesium-Überschuss tut ein Übriges, um Nebenreaktionen zu unterbinden: Die Ausgangssubstanz reagiert eher mit dem reichlich vorhandenen Magnesium als mit dem rasch abgeführten Produkt.
Pilotanlage: Skalierbar und flexibel
Eine Pilotanlage haben die Forscher bereits realisiert: Bis zu 20 Liter Ausgangslösung setzt sie pro Stunde um. Je nach benötigter Menge kann diese nur kurzzeitig betrieben werden oder aber rund um die Uhr laufen. Werden noch größere Mengen benötigt, lassen sich auch mehrere Reaktormodule gleichzeitig betreiben – die Pilotanlage besteht derzeit aus vier solcher Module. Sie ist gleichzeitig ein essentieller Zwischenschritt hin zu noch höheren Durchsätzen bzw. hin zum Industrieproduktionsmaßstab. Auch erste Machbarkeitsstudien mit Industriepartnern haben die Fraunhofer-Experten bereits durchgeführt. »In die gesamte Entwicklung vom Labormaßstab bis hin zur Pilotanlage flossen Rückmeldungen aus der Industrie ein«, bestätigt Menges-Flanagan. Eine Pilotierung bei Industriekunden sei in etwa einem Jahr denkbar.
Die Anlage funktioniert jedoch nicht nur für alle erdenklichen Grignard-Reagenzien, sondern lässt sich langfristig auch für die Zink-Organometall-Synthese nutzen. Im Labormaßstab haben die Forscher diese Reaktionen bereits durchgeführt. Der neue Reaktor soll es erstmalig erlauben, auch diese Reaktion optimal skalieren zu können.
Weitere News aus dem Ressort Wissenschaft
Diese Produkte könnten Sie interessieren

Redeem continuous-flow Photoreactor von Redeem Solar Technologies
Skalierbare, grüne und effiziente Synthese mit dem Redeem Photoreaktor
Der neue Redeem Photoreaktor eröffnet einzigartige Möglichkeiten in der Welt der chemischen Synthese
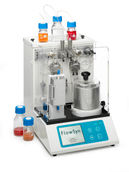
FlowSyn and FlowSyn Maxi von Uniqsis
Kontinuierliche Flow Chemistry Systeme für Reaktionsoptimierung und Scale-up
Durchführung von Reaktionen bis zu 300°C und 100 bar von 0,1 - 100 ml /Minute
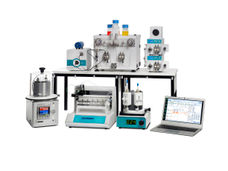
FlowLab Plus von Uniqsis
Vielseitiges Modulares Durchflussreaktorsystem
Flexibles, modular aufgebautes Flow Chemistry-System mit “Plug-and-Play”-Funktion
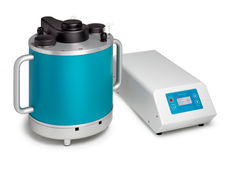
PhotoSyn™ von Uniqsis
Erleben Sie die Zukunft der Photochemie
Durchflussreaktor mit intuitiver Steuerung für höhere Ausbeuten und höhere Selektivität
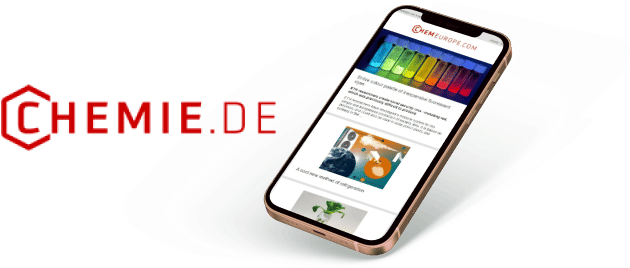
Holen Sie sich die Chemie-Branche in Ihren Posteingang
Mit dem Absenden des Formulars willigen Sie ein, dass Ihnen die LUMITOS AG den oder die oben ausgewählten Newsletter per E-Mail zusendet. Ihre Daten werden nicht an Dritte weitergegeben. Die Speicherung und Verarbeitung Ihrer Daten durch die LUMITOS AG erfolgt auf Basis unserer Datenschutzerklärung. LUMITOS darf Sie zum Zwecke der Werbung oder der Markt- und Meinungsforschung per E-Mail kontaktieren. Ihre Einwilligung können Sie jederzeit ohne Angabe von Gründen gegenüber der LUMITOS AG, Ernst-Augustin-Str. 2, 12489 Berlin oder per E-Mail unter widerruf@lumitos.com mit Wirkung für die Zukunft widerrufen. Zudem ist in jeder E-Mail ein Link zur Abbestellung des entsprechenden Newsletters enthalten.