Einsatz künstlicher Intelligenz zur Steuerung der digitalen Fertigung
Forscher trainieren ein maschinelles Lernmodell zur Überwachung und Anpassung des 3D-Druckprozesses, um Fehler in Echtzeit zu korrigieren
Wissenschaftler und Ingenieure entwickeln ständig neue Materialien mit einzigartigen Eigenschaften, die für den 3D-Druck verwendet werden können, aber herauszufinden, wie mit diesen Materialien zu drucken ist, kann ein komplexes, kostspieliges Rätsel sein.
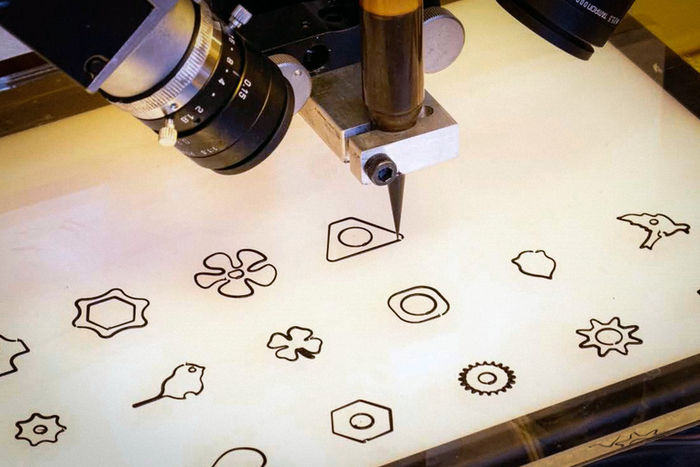
MIT-Forscher haben ein Machine-Learning-Modell trainiert, um den 3D-Druckprozess in Echtzeit zu überwachen und anzupassen.
Courtesy of Wojciech Matusik, Mike Foshey, et al
Oft muss ein erfahrener Bediener durch manuelles Ausprobieren - möglicherweise nach Tausenden von Druckvorgängen - die idealen Parameter ermitteln, mit denen sich ein neues Material konsistent und effektiv drucken lässt. Zu diesen Parametern gehören die Druckgeschwindigkeit und die Materialmenge, die der Drucker aufträgt.
MIT-Forscher haben nun künstliche Intelligenz eingesetzt, um dieses Verfahren zu rationalisieren. Sie haben ein maschinelles Lernsystem entwickelt, das den Herstellungsprozess mit Hilfe von Computer-Vision beobachtet und dann Fehler in der Materialverarbeitung in Echtzeit korrigiert.
Mithilfe von Simulationen brachten sie einem neuronalen Netzwerk bei, wie es die Druckparameter anpassen muss, um Fehler zu minimieren, und wendeten diese Steuerung dann auf einen echten 3D-Drucker an. Ihr System druckte Objekte genauer als alle anderen 3D-Drucksteuerungen, mit denen sie es verglichen.
Die Arbeit vermeidet das unerschwingliche Verfahren, Tausende oder Millionen echter Objekte zu drucken, um das neuronale Netzwerk zu trainieren. Außerdem könnten Ingenieure auf diese Weise leichter neue Materialien in ihre Drucke einbauen und so Objekte mit besonderen elektrischen oder chemischen Eigenschaften entwickeln. Es könnte den Technikern auch dabei helfen, den Druckprozess im Handumdrehen anzupassen, wenn sich Material oder Umgebungsbedingungen unerwartet ändern.
"Dieses Projekt ist die erste Demonstration eines Fertigungssystems, das mit Hilfe von maschinellem Lernen eine komplexe Steuerungsstrategie erlernt", sagt der Hauptautor Wojciech Matusik, Professor für Elektrotechnik und Informatik am MIT und Leiter der Computational Design and Fabrication Group (CDFG) innerhalb des Computer Science and Artificial Intelligence Laboratory (CSAIL). "Wenn man intelligentere Fertigungsmaschinen hat, können sie sich in Echtzeit an die sich verändernde Umgebung am Arbeitsplatz anpassen, um die Ausbeute oder die Genauigkeit des Systems zu verbessern. Man kann mehr aus der Maschine herausholen".
Die Co-Autoren sind Mike Foshey, Maschinenbauingenieur und Projektleiter bei der CDFG, und Michal Piovarci, Postdoc am Institute of Science and Technology in Österreich. Zu den MIT-Koautoren gehören Jie Xu, ein Doktorand der Elektrotechnik und Informatik, und Timothy Erps, ein ehemaliger technischer Mitarbeiter der CDFG. Die Forschungsergebnisse werden auf der SIGGRAPH-Konferenz der Association for Computing Machinery vorgestellt.
Die Auswahl der Parameter
Die Bestimmung der idealen Parameter für einen digitalen Fertigungsprozess kann einer der teuersten Teile des Prozesses sein, weil so viel Versuch und Irrtum erforderlich ist. Und wenn ein Techniker eine Kombination gefunden hat, die gut funktioniert, sind diese Parameter nur für eine bestimmte Situation ideal. Er hat kaum Daten darüber, wie sich das Material in anderen Umgebungen oder auf anderer Hardware verhält oder ob eine neue Charge andere Eigenschaften aufweist.
Die Verwendung eines maschinellen Lernsystems ist ebenfalls mit Herausforderungen verbunden. Zunächst mussten die Forscher messen, was im Drucker in Echtzeit passiert.
Zu diesem Zweck entwickelten sie ein Machine-Vision-System mit zwei Kameras, die auf die Düse des 3D-Druckers gerichtet sind. Das System beleuchtet das Material, während es aufgetragen wird, und berechnet anhand der Lichtmenge, die durchgelassen wird, die Dicke des Materials.
"Man kann sich das Bildverarbeitungssystem wie eine Reihe von Augen vorstellen, die den Prozess in Echtzeit beobachten", sagt Foshey.
Die Steuerung würde dann die Bilder verarbeiten, die sie vom Bildverarbeitungssystem erhält, und auf der Grundlage der erkannten Fehler die Vorschubgeschwindigkeit und die Richtung des Druckers anpassen.
Das Training einer auf einem neuronalen Netz basierenden Steuerung, die diesen Fertigungsprozess versteht, ist jedoch sehr datenintensiv und würde Millionen von Drucken erfordern. Daher bauten die Forscher stattdessen einen Simulator.
Erfolgreiche Simulation
Um ihre Steuerung zu trainieren, verwendeten sie ein Verfahren, das als Verstärkungslernen bekannt ist, bei dem das Modell durch Versuch und Irrtum mit einer Belohnung lernt. Das Modell hatte die Aufgabe, Druckparameter auszuwählen, die ein bestimmtes Objekt in einer simulierten Umgebung erzeugen würden. Nachdem dem Modell das erwartete Ergebnis gezeigt wurde, wurde es belohnt, wenn die von ihm gewählten Parameter den Fehler zwischen seinem Druck und dem erwarteten Ergebnis minimierten.
In diesem Fall bedeutet ein "Fehler", dass das Modell entweder zu viel Material aufgetragen hat, so dass es in Bereichen platziert wurde, die hätten offen bleiben sollen, oder dass es zu wenig Material aufgetragen hat, so dass offene Stellen zurückblieben, die aufgefüllt werden sollten. Je mehr simulierte Drucke das Modell durchführte, desto genauer wurde es, um die Belohnung zu maximieren.
Die reale Welt ist jedoch unordentlicher als eine Simulation. In der Praxis ändern sich die Bedingungen in der Regel durch geringfügige Abweichungen oder Rauschen im Druckprozess. Daher haben die Forscher ein numerisches Modell erstellt, das das Rauschen des 3D-Druckers annähernd berücksichtigt. Anhand dieses Modells fügten sie der Simulation Rauschen hinzu, was zu realistischeren Ergebnissen führte.
"Das Interessante war, dass wir durch die Implementierung dieses Geräuschmodells in der Lage waren, die rein in der Simulation trainierte Steuerungsstrategie auf die Hardware zu übertragen, ohne sie durch physische Experimente zu trainieren", sagt Foshey. "Wir brauchten danach keine Feinabstimmung an der tatsächlichen Anlage vorzunehmen."
Als sie das Steuergerät testeten, druckte es Objekte genauer als jede andere von ihnen untersuchte Steuerungsmethode. Besonders gut schnitt er beim Infill-Druck ab, bei dem das Innere eines Objekts gedruckt wird. Bei anderen Steuerungen wurde so viel Material aufgetragen, dass sich das gedruckte Objekt ausbeulte, aber die Steuerung der Forscher passte den Druckpfad so an, dass das Objekt eben blieb.
Die Steuerung kann sogar lernen, wie sich das Material nach dem Auftragen verteilt und die Parameter entsprechend anpassen.
"Wir waren auch in der Lage, Steuerungsrichtlinien zu entwickeln, die verschiedene Materialtypen on-the-fly steuern können. Wenn Sie also einen Fertigungsprozess im Feld hatten und das Material ändern wollten, mussten Sie den Fertigungsprozess nicht erneut validieren. Man kann einfach das neue Material laden, und die Steuerung passt sich automatisch an", sagt Foshey.
Nachdem sie die Wirksamkeit dieser Technik für den 3D-Druck nachgewiesen haben, wollen die Forscher nun Steuerungen für andere Fertigungsverfahren entwickeln. Außerdem möchten sie herausfinden, wie der Ansatz für Szenarien modifiziert werden kann, in denen mehrere Materialschichten oder mehrere Materialien auf einmal gedruckt werden. Außerdem ging ihr Ansatz davon aus, dass jedes Material eine feste Viskosität ("Sirupartigkeit") hat. In einer zukünftigen Version könnte jedoch KI eingesetzt werden, um die Viskosität in Echtzeit zu erkennen und anzupassen.
Hinweis: Dieser Artikel wurde mit einem Computersystem ohne menschlichen Eingriff übersetzt. LUMITOS bietet diese automatischen Übersetzungen an, um eine größere Bandbreite an aktuellen Nachrichten zu präsentieren. Da dieser Artikel mit automatischer Übersetzung übersetzt wurde, ist es möglich, dass er Fehler im Vokabular, in der Syntax oder in der Grammatik enthält. Den ursprünglichen Artikel in Englisch finden Sie hier.