Schädlichen Spannungen auf der Spur: Metall- und Kunststoffteile im Stresstest
Wie lange ein Werkzeug „lebt", wie gut eine Turbine oder ein Zahnrad die Dauerbelastungen des Betriebsalltags aushält, hängt entscheidend vom Herstellungsprozess ab. Am Fachbereich Maschinenbau der Universität Kassel entwickeln Wissenschaftler deshalb im Rahmen eines Sonderforschungsprojektes der Deutschen Forschungsgemeinschaft (DFG) neuartige und kostengünstigere Produktionsabläufe für robuste Bauteile.
„Holz arbeitet" heißt es. Doch das gilt auch für Metalle, Verbundmaterialien und Kunststoffe. Bei der Herstellung von Flanschen, Wellen oder Zahnrädern entstehen beim Härtungsprozess durch die Einwirkung von Druck, Reibung und Hitze unerwünschte Spannungen im Material. Das ist besonders fatal, wenn es sich um gradierte Werkzeuge oder Bauteile handelt, also solche, die unterschiedliche Belastungen aushalten und verschiedene Funktionen gleichzeitig erfüllen sollen. So muss ein Zahnrad außen möglichst hart, innen aber weich und zäh sein. „Stimmt die Härteverteilung nicht, werden die Zähne schnell spröde und können abbrechen", so Professor Dr. Berthold Scholtes vom Institut für Werkstofftechnik an der Universität.
Der Wissenschaftler forscht an einer wichtigen Schnittstelle des 20 Teilprojekte umfassenden Sonderforschungsprogramms TRR 30 der DFG, bei dem die Universität Kassel eng mit den Hochschulen in Dortmund und Paderborn zusammenarbeitet. Denn auf dem Weg zu einer rationelleren Produktion und zugleich verschleißärmeren Bauteilen und Werkzeugen ist die Analyse der Spannungen, die bei unterschiedlichen Herstellungsprozessen unter dem Einfluss von Temperatur und mechanischen Belastungen entstehen, ein Schlüssel zum Erfolg.
Professor Scholtes unterscheidet Druck- und Zugspannungen im Gefüge eines Werkzeugs oder Bauteils. Schädlich sind die letzteren, weil sie die Lebensdauer eines Bauteils verkürzen und ein Werkzeug vorzeitig stumpf und unbrauchbar machen. Doch sie entstehen gerade durch die nötige Härtung des Stahls oder durch die Reibungshitze, die verursacht wird, wenn ein Werkzeug ein neues Bauteil bearbeitet. Die Kunst besteht darin, schon durch die Art des Fertigungsprozesses die unerwünschten Zugspannungen zu minimieren. Die erwünschten Druckspannungen an der Oberfläche des Materials kann man durch eine Änderung der Temperaturmaxima während der Abkühlungs- und Erhitzungsprozesse beim Härten oder auch durch nachträgliches Schleifen an den gewünschten Stellen erhöhen. Im Labor des Instituts werden Proben von experimentell hergestellten gradierten Materialien wochenlangen Stresstests unterzogen und die Verteilung der Spannungen im Röntgendiffraktometer untersucht.
Das Institut hat bereits vor dem Start des DFG-Projekts vor vier Jahren viele Erfahrungen auf diesem Gebiet gesammelt: Eine Reihe von Firmen lassen Bauteile oder Werkzeuge, die überraschend frühzeitig unbrauchbar geworden sind, im Labor der Materialforscher testen, berichtet Professor Scholtes. Fernziel seiner Forschung ist nicht nur die Herstellung von neuartigen Bauteilen mit flexiblen Eigenschaften sondern auch eine kostengünstigere Fertigung. „Wir wollen Prozessschritte einsparen", sagt der Wissenschaftler. Für ein Hochlohnland wie Deutschland ist das ein wichtiger Wirtschaftsfaktor, da Bauteile aus einem Guss Energie und Arbeitszeit sparen. Ein Zahnrad könnte, so hofft Professor Scholtes, bald in einem Produktionsschritt hergestellt werden. Momentan benötigt man noch mehrere. Die DFG sieht die Forscher offenbar auf gutem Weg dorthin. Sie hat den Forschungsauftrag für die Kasseler Uni, der mit etwa 2,5 Millionen Euro jährlich dotiert ist, bis 2014 verlängert.
Meistgelesene News
Themen
Organisationen
Weitere News aus dem Ressort Wissenschaft
Diese Produkte könnten Sie interessieren
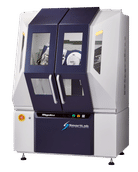
SmartLab von Rigaku
SmartLab - Hochfluss-Mehrzweck-XRD – Das leistungsstärkste laborgestützte XRD-Gerät auf dem Markt
XtaLAB Single von Rigaku
Präzise Kristallstrukturanalyse für Moleküle und Proteine
Flexible XRD-Geräte mit einfacher Bedienung und höchster Leistung

MiniFlex von Rigaku
Materialanalyse neu definiert: Das Rigaku MiniFlex Tisch-Röntgendiffraktometer
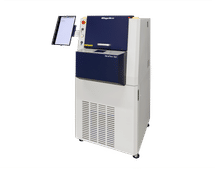
Miniflex XpC von Rigaku
Miniflex XpC - XRD für die Qualitätskontrolle mit hohem Durchsatz
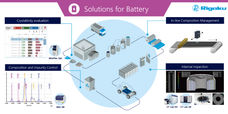
Lösungen für die Batterieforschung von Rigaku
Entdecken Sie das Potenzial von Batterien mit modernster Messtechnik
Optimieren Sie Ihre Batterieforschung durch den Einsatz innovativer Röntgentechnologien
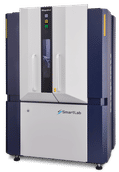
SmartLab SE von Rigaku
Intelligente Röntgenanalyse für Forschung und Qualitätssicherung
Maximieren Sie Ihre Produktivität mit automatisierten Prozessen und vielfältigem Zubehör
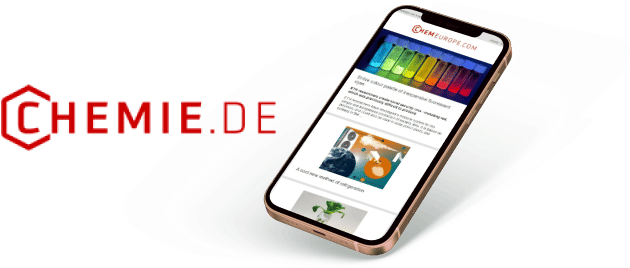
Holen Sie sich die Chemie-Branche in Ihren Posteingang
Mit dem Absenden des Formulars willigen Sie ein, dass Ihnen die LUMITOS AG den oder die oben ausgewählten Newsletter per E-Mail zusendet. Ihre Daten werden nicht an Dritte weitergegeben. Die Speicherung und Verarbeitung Ihrer Daten durch die LUMITOS AG erfolgt auf Basis unserer Datenschutzerklärung. LUMITOS darf Sie zum Zwecke der Werbung oder der Markt- und Meinungsforschung per E-Mail kontaktieren. Ihre Einwilligung können Sie jederzeit ohne Angabe von Gründen gegenüber der LUMITOS AG, Ernst-Augustin-Str. 2, 12489 Berlin oder per E-Mail unter widerruf@lumitos.com mit Wirkung für die Zukunft widerrufen. Zudem ist in jeder E-Mail ein Link zur Abbestellung des entsprechenden Newsletters enthalten.