Magnetisch gelagerter Verdichter für Siliziumherstellung durch die Pyrolyse von Monosilan
Durch den verstärkten Einsatz von Solarzellen ist die Nachfrage nach Polysilizium in den letzten Jahren stark angestiegen. Um den Bedarf decken zu können, entwickelte ein Unternehmen ein neues Produktionsverfahren, das auch eine komplett neue Peripherie verlangt. Dafür konstruierte und baute FIMA Maschinenbau einen magnetgelagerten Verdichter, der Wasserstoff zirkuliert.
Beim herkömmlichen Produktionsprozess wird Rohsilizium über die Zwischenstufe Trichlorsilan in aufwändigen Destillationsschritten von Verunreinigungen befreit. Dieses energiereiche Verfahren soll nun durch die Pyrolyse von Monosilan abgelöst werden. Der aggressive Chlorwasserstoff wird für diesen Herstellungsprozess nicht mehr benötigt. Das im Labormaßstab funktionierende Verfahren wird derzeit großtechnisch umgesetzt.
In einem Reaktor zerfällt bei hohen Temperaturen Monosilan in reines Silizium und in Wasserstoff – ein Teil des Gases wird dem System entzogen und neues Monosilan zugegeben. An zuvor eingebrachten Keimstäben setzt sich das polykristalline Silizium ab, das dann alle fünf bis sechs Tage „geerntet“ werden kann. Da der Prozess im Kreislauf gefahren und hochreines Silizium gewonnen wird, sind spezielle Verdichter gefragt, die keine Partikel generieren und keine Fremdmoleküle eindringen lassen.
FIMA Maschinenbau entwickelte für dieses Vorhaben einen zweistufigen Verdichter, der zunächst in einer Pilotanlage eingesetzt wird. Die Anforderungen sind ein abgeschlossenes System, das keine Verunreinigungen generiert und keine eindringen lässt. Außerdem darf durch den Verdichter innerhalb des Wasserstoffkreislaufes keine explosive Atmosphäre entstehen. Ein konventioneller Aufbau des Verdichters mit Dichtungen, angetrieben mittels Getriebe und Motor, schied aus, da jegliche berührenden Dichtungen, auch Gleitringdichtungen, geringste Mengen Partikel in das Wasserstoffgassystem emittieren würden. Somit musste der Verdichter hermetisch geschlossen werden, der komplette Antrieb kam in den Wasserstoffprozessraum.
Somit entfallen alle dynamischen Abdichtungen, es sind nur noch statische Dichtungen und Kabeldurchführungen vorhanden, die keine Partikel generieren. Wenn sich der komplette Antrieb im Wasserstoffprozessbereich befindet, ist eine konventionelle Lagerung aufgrund der Verunreinigung durch Schmierstoffe ausgeschlossen – eine magnetgelagerte Welle schafft Abhilfe. Die Welle wird durch die Magnetlager im Wasserstoffgas sowohl im Stillstand als auch bei hohen Drehzahlen im Schwebezustand gehalten.
Nach dem Bau des Prototyps wurde die Anlage im firmeneigenen Testfeld auf Herz und Nieren geprüft. Die Ingenieure bauten eine Kreisgasanlage, um die tatsächlichen Einsatzbedingungen mittels Helium zu simulieren.
Organisationen
Weitere News aus dem Ressort Forschung & Entwicklung
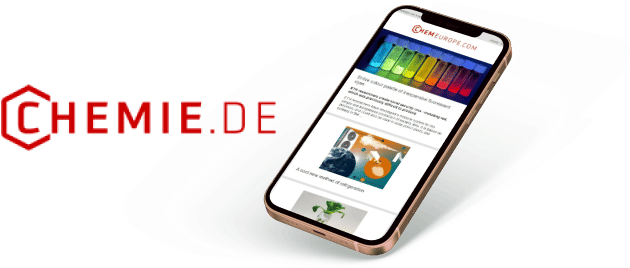
Holen Sie sich die Chemie-Branche in Ihren Posteingang
Mit dem Absenden des Formulars willigen Sie ein, dass Ihnen die LUMITOS AG den oder die oben ausgewählten Newsletter per E-Mail zusendet. Ihre Daten werden nicht an Dritte weitergegeben. Die Speicherung und Verarbeitung Ihrer Daten durch die LUMITOS AG erfolgt auf Basis unserer Datenschutzerklärung. LUMITOS darf Sie zum Zwecke der Werbung oder der Markt- und Meinungsforschung per E-Mail kontaktieren. Ihre Einwilligung können Sie jederzeit ohne Angabe von Gründen gegenüber der LUMITOS AG, Ernst-Augustin-Str. 2, 12489 Berlin oder per E-Mail unter widerruf@lumitos.com mit Wirkung für die Zukunft widerrufen. Zudem ist in jeder E-Mail ein Link zur Abbestellung des entsprechenden Newsletters enthalten.