Aluminiumoxid aus der Flamme macht Glasoberflächen korrosionsbeständig
Wasserbeständigkeit von Kalk-Natron-Glas reicht durch Oberflächenmodifikation an die von Borosilikatglas heran
Glas ist ein recht dauerhafter Werkstoff. Seine Oberfläche kann jedoch langsam durch Wasser zerstört werden, auch bekannt als Glaskorrosion. Wissenschaftlern des INNOVENT Technologieentwicklung e.V. in Jena ist es jetzt gelungen, die Korrosionsbeständigkeit von Glas durch ein einfaches und kostengünstiges Verfahren der Oberflächenmodifikation erheblich zu verbessern. Billiges Kalk-Natron-Glas wird damit so wasserbeständig wie teures Borosilikatglas.
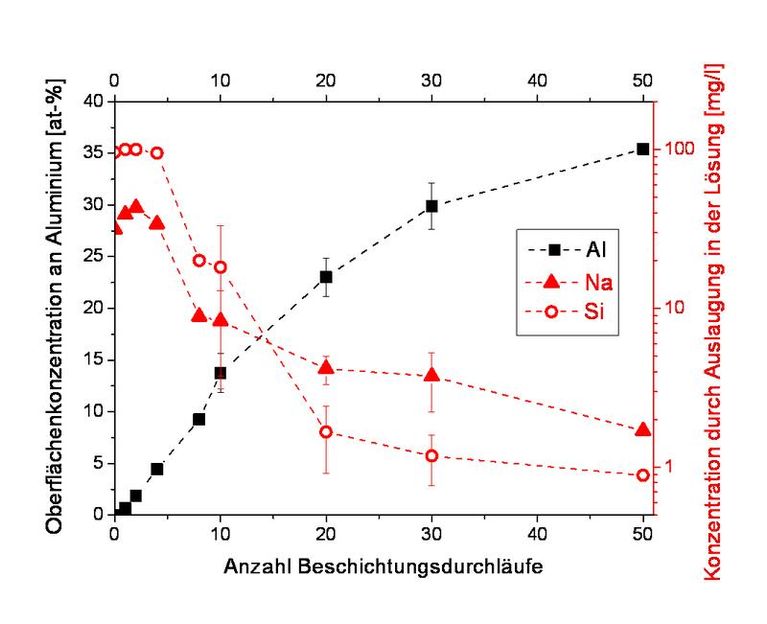
Oberflächenkonzentration an Aluminium und ausgelaugte Konzentration an Silicium und Natrium
INNOVENT, Jena
Glas korrodiert, auch wenn es mit bloßem Auge über lange Zeit nicht wahrzunehmen ist. Vor allem an technische Gläser werden hohe Anforderungen hinsichtlich Transmission und Lichtstreuung gestellt, die sie auch unter schwierigen Bedingungen, wie ungünstigem Klima oder in Kontakt mit auslaugenden Flüssigkeiten (z.B. Wasser), einhalten sollen. Auslaugungsprozesse verändern die Zusammensetzung der Glasoberfläche z.B. durch ein Herauslösen von Alkalien und Silizium und führen beim Fortschreiten des Prozesses zum Abbau der Glasmatrix. Das Glas kann dadurch trüb werden.
Kalk-Natron-Gläser sind weit verbreitet, relativ günstig in der Herstellung, jedoch unbefriedigend in ihrer Korrosionsbeständigkeit. Durch Zusatz verschiedener Metalloxide (z.B. von Aluminium, Zirkon, Zink oder Bor) läßt sich ihre Beständigkeit erhöhen, es erhöht die Herstellungskosten jedoch auch.
In Jena geht man jetzt neue Wege. Anstatt die Metalloxide im gesamten Glaskörper zu verteilen, bringen die Wissenschaftler des INNOVENT Technologieentwicklung e.V. sie nur an der Oberfläche auf, denn nur die Oberfläche ist den Angriffen ausgesetzt.
Dabei setzten die Jenenser auf eine Weiterentwicklung der etablierten Flammenpyrolyse. Bei diesem Verfahren, das auch unter dem Namen „Combustion Chemical Vapour Deposition (CCVD) bekannt ist, wird eine Flamme über die zu funktionalisierende Oberfläche geführt. Dem Brenngas werden dabei geringe Mengen an Chemikalien („Precursoren“) zugesetzt, die in der Flamme hochreaktive Verbindungen bilden und durch Vernetzung mit der Oberfläche eine neue Schicht bilden. Die einfache und kostengünstige Flammenpyrolyse wird seit Jahren weltweit mit Erfolg zur Erzeugung funktioneller Schichten eingesetzt, die z.B. transmissionserhöhend oder haftungsverbessernd wirken.
Bei der jetzt neu entwickelten Variante wird eine aluminiumhaltige Vorläufersubstanz verwendet, die nach der Reaktion in der Flamme als Aluminiumoxid in die Glasoberfläche eingebaut wird. Für dieses Verfahren können die meisten der bereits heute eingesetzten Anlagen zur Flammenpyrolyse ohne größere Veränderungen eingesetzt werden. Lediglich ein zusätzliches Erwärmen des Glases wird zur Qualitätsverbesserung empfohlen.
Bereits der Einbau geringer Mengen Aluminiumoxid führt zu deutlich erhöhter Beständigkeit gegen Auslaugung durch Wasser; eine vollständige „Bedeckung“ mit Aluminiumoxid ist dafür nicht nötig. Damit reichen kurze Behandlungszeiten, was eine kostengünstige Integration des Verfahrens in laufende Produktionsprozesse ermöglicht und die sonstigen Materialeigenschaften (Bruchstabilität, Transmission, etc.) nur unwesentlich verändert. Mit dieser flammenpyrolytischen Aluminiumoxidbeschichtung kann eine einhundertfache Verbesserung der Beständigkeit von Kalk-Natron-Glas erreicht werden. Es ist dann ebenso wasserbeständig wie die deutlich teureren Borosilikatgläser. Für Anwendungen wie in der Solartechnik ist dabei von Interesse, dass die Transmission des Flachglases durch die Behandlung maximal um 0,5 % sinkt.
Meistgelesene News
Organisationen
Weitere News aus dem Ressort Forschung & Entwicklung
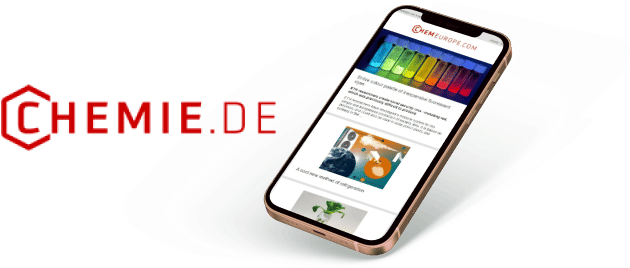
Holen Sie sich die Chemie-Branche in Ihren Posteingang
Mit dem Absenden des Formulars willigen Sie ein, dass Ihnen die LUMITOS AG den oder die oben ausgewählten Newsletter per E-Mail zusendet. Ihre Daten werden nicht an Dritte weitergegeben. Die Speicherung und Verarbeitung Ihrer Daten durch die LUMITOS AG erfolgt auf Basis unserer Datenschutzerklärung. LUMITOS darf Sie zum Zwecke der Werbung oder der Markt- und Meinungsforschung per E-Mail kontaktieren. Ihre Einwilligung können Sie jederzeit ohne Angabe von Gründen gegenüber der LUMITOS AG, Ernst-Augustin-Str. 2, 12489 Berlin oder per E-Mail unter widerruf@lumitos.com mit Wirkung für die Zukunft widerrufen. Zudem ist in jeder E-Mail ein Link zur Abbestellung des entsprechenden Newsletters enthalten.