Aus Schaum gedruckte Keramik
ETH-Forschende haben mithilfe eines additiven Fertigungsverfahrens ein äusserst poröses Keramik-Bauteil gedruckt. Ein solches Material mit einem 3D-Drucker herzustellen, ist ein Kunststück.
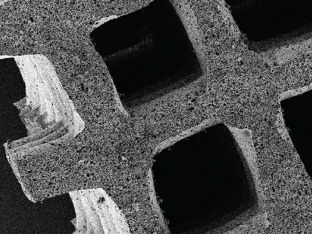
Das Elektronenmikroskop bringt die Feinstruktur des 3D-gedruckten Keramikschaums ans Licht.
Bild: aus Minas et al, 2016, Adv. Materials
Die Doktorandin Carla Minas aus der Gruppe für Komplexe Materialien von ETH-Professor André Studart hat ein hoch poröses und dennoch äusserst robustes Keramikmaterial geschaffen. Sie hat dieses mit einem additiven Fertigungsverfahren «gedruckt». Die Kunst dabei war es, eine stabile Keramikemulsion als «Tinte» zu verwenden, die während und nach dem Drucken nicht in sich zusammenfällt. Mit dieser Technik lassen sich komplexe poröse Strukturen herstellen, wie sie auch in der Natur in der Form von Knochen oder Kieselalgen vorzufinden sind.
Das Verfahren sowie den resultierenden Keramikschaum haben die Materialforschenden soeben in der Fachzeitschrift «Advanced Materials» veröffentlicht.
Mit Öl und Küchenmixer zum druckbaren Schaum
Für das 3D-Drucken verwendete die Forscherin eine Emulsion beziehungsweise einen Schaum, der aus einer wässrigen Lösung, Keramik-Partikeln aus Aluminiumoxid (Al2O3) und bestimmten Zusätzen besteht. Beim Schaum sind die Bläschen mit Luft gefüllt, bei der Emulsion mit Öltröpfchen. Sowohl den Schaum als auch die Emulsion können die Forschenden zum Drucken verwenden. Die beiden Formen führen aber zu unterschiedlichen Porengrößen.
Schon früher entwickelten Forschende in Studarts Labor die dem Verfahren zugrunde liegende Suspension. Daraus stellte Minas unter Zugabe von Öl und durch kräftiges Rühren eine Emulsion her. Dabei entstanden Öltröpfchen verschiedener Grösse, welche von Keramikteilchen umgeben sind. Die Keramikteilchen wurden dabei so verändert, dass sie sich bevorzugt an der Oberfläche der Tröpfchen befinden. Dieser Mantel aus Partikeln stabilisiert die Tröpfchen und verhindert deren Verschmelzen mit benachbarten Tröpfchen. Ein hoher Anteil von Öl erzeugt ein dichtes Netzwerk aus stabilisierten Tröpfchen. Das Keramikgerüst verhindert ausserdem, dass die Porenstruktur beim Trocknen und Brennen zerstört wird.
Viskosität nimmt mit Öl- und Partikelgehalt zu
Dieses Netzwerk ist die Grundlage für die spezifischen Fliesseigenschaften, die für das 3D Drucken benötigt werden. Auch lässt sich die Tröpfchengrösse und damit der künftige Porenraum einstellen. «Dies hängt von der Viskosität der Masse ab. Je grösser der Partikel- und der Ölgehalt, desto viskoser wird die Keramikemulsion und desto kleiner werden die Tröpfchen», erklärt Minas.
Als weiteren Zusatz verwendete sie Polyvinylalkohol (PVA), ein kurzes Polymer. Auch dieses lagerte sich bevorzugt an der Grenzfläche von Öl und Wasser an und verdrängte dabei Partikel aus dem Keramikmantel, der die Tröpfchen umgibt. Die PVA-Moleküle wirken als Platzhalter für haarfeine Kanäle, welche benachbarte Tröpfchen miteinander verbinden.
Mit Direct Ink Writing (DIW), einer verbreiteten additiven Fertigungstechnik, druckte die Materialforscherin schliesslich mit der Keramik-Emulsion eine dreidimensionale Gitterstruktur. Diese wurde bei Raumtemperatur getrocknet und anschliessend im Brennofen bei 1600°C gehärtet. Beim Trocknen verdampfte das Öl, das Brennen vernichtete die PVA-Moleküle und verdichtete den Keramikmantel um die Poren. Ein hartes Keramikgerüst blieb zurück, bei dem die Porenstruktur des Schaums perfekt erhalten bliebt.
Poren verbinden Poren
Das Keramikgerüst weist Poren in bis zu drei Grössenordnungen auf: Die grössten Poren werden durch die Gitterstruktur mit einer frei wählbaren Maschenweite gebildet. Die Öltröpfchen erzeugen die nächste Stufe von Poren, und die kleinsten Poren entstehen durch das PVA. Der Porenanteil beträgt bis zu 95 Prozent des Materialvolumens. Dennoch ist das Material mechanisch äusserst robust, wie Belastungstests zeigen.
«Bisher wurden Gitterstrukturen, deren Filamente keine Poren haben, ebenfalls als Schaum bezeichnet», sagt André Studart. Ihre Struktur sei aber wirklich porös, da jedes Filament selbst porös sei und die Poren wiederum durch Poren miteinander verbunden seien. «Für solche Materialien gibt es natürliche Vorbilder: Knochen, Bambus oder Holz sind nach einem vergleichbaren Prinzip aufgebaut», sagt der ETH-Professor.
Das Prinzip des 3D-Druckens von keramisch stabilisierten Emulsionen und Schäumen kann nicht nur für Aluminiumoxid, sondern auch verschiedene andere Keramiken genutzt werden. Die Forscherin konnte zudem in einem Druckvorgang mehrere «Tinten» kombinieren. Dadurch konnte sie komplexe Strukturen mit unterschiedlichen Materialteilungen herstellen. Je nach Anwendung können so das Material und dessen Struktur optimiert werden, um eine möglichst hohe Leistung zu erzielen.
Geeignet für die Industrie
Das Ziel dieser Forschungsarbeit war, ein Material zu schaffen, das bei minimalem Materialaufwand eine maximale mechanische Festigkeit hat; Eigenschaften, die Leichtbau-Materialen haben müssen. Dank der hohen Porosität ist darüber hinaus ein maximaler Durchfluss durch eine Struktur mit grosser Oberfläche möglich. Keramikstrukturen, die mit dieser Methode hergestellt werden, würden sich deshalb gut für Anwendungen als Katalysator in der chemischen Industrie, in der Biomedizin oder im Energiesektor eignen.
Für letzteren haben Studarts Forschende diesen Keramikschaum auch entwickelt: Das IBM Research Center in Rüschlikon (ZH) erforscht derzeit intensiv Möglichkeiten, Restwärme zum Wärmen und Kühlen von Häusern zu verwenden, ohne dabei weitere Energie zu benötigen. Dazu werden Materialien gebraucht, die hoch effizient Wasser aufnehmen können und dabei Wärme abgeben. Das Drucken von Emulsionen oder Schäumen ermöglicht die optimale Architektur eines solchen Materials.